In a world where the demand for clean water is increasingly strained by burgeoning populations and environmental pressures, the quest for innovative solutions has become paramount. In recognition of the evolving needs of manufactures that make the products we rely on and the recyclers trying to reduce waste, ElectraMet technology was created as a metal separations company for industrial applications struggling with dissolved metal impurities. While initially developed to address concerns with lead in drinking water, ElectraMet quickly evolved based on customer inquiries regarding how to remove copper from industrial production fluids and waste streams. “We quickly pivoted to industrial applications where we found our solution could have a transformative impact, particularly in addressing copper-laden waste streams,” explains Dr. Cameron Lippert, Co-Founder and Chief Innovation Officer at ElectraMet.
ElectraMet was established on the principle of leveraging ubiquitous carbon materials and electrochemical processes to solve real-world separation challenges. Driven by microelectronics’ & surface finishings’ need to comply with effluent limitation guidelines and water recycling objectives, the company has applied its innovative and highly selective technology to onsite removal and recovery aligned with discharge compliance requirements, constricting operating budgets, and a push towards reducing carbon footprint.
“Embedded within our design philosophy is a commitment to sustainability,” affirms Dr. Lippert, a seasoned entrepreneur with over a decade of experience in developing and commercializing innovations. Before his entrepreneurial endeavors, Dr. Lippert spearheaded multimillion-dollar technology projects at the Center for Applied Energy Research, spanning from carbon capture to advanced battery chemistry. Central to ElectraMet’s ethos is simplicity in system design, a natural ally to sustainability, lowering barriers to entry for new water treatment technologies and facilitating widespread adoption. Leveraging the efficiency of electrochemistry, ElectraMet streamlines processes, achieving results in fewer steps than traditional methods, and thereby driving their mission forward.
A Versatile Solution for Comprehensive Metal Recovery
ElectraMet’s engineering allows for removal and recovery across all concentration ranges for copper, which separates it from traditional solutions that solely focus on either low or high concentrations, such as ion-exchange, chemical precipitation, or electrowinning. This broad applicability for copper presents outstanding application in microelectronics and battery recycling applications. These market segments see exceptional value in ElectraMet’s automation, data accessibility, removal process verification, and onsite metal recovery. The elimination of hauling combined with onsite recovery of solid recyclable metal provides tremendous carbon footprint reduction.
“For battery recycling, we not only eliminate impurities but also offer real-time monitoring to ensure that product purity or discharge compliance meets specification,” explains Dr. Lippert. “ElectraMet solutions enhance product value through removing copper and manganese impurities from process streams or recovering valuable metals from wastewater discharge and assuring compliance. Either way, both the customer and environment win. We enable companies to do the right thing the right way.”
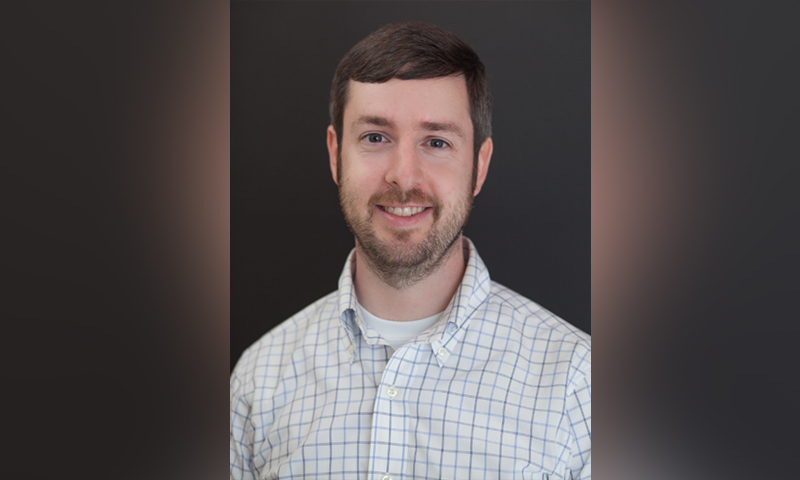
Within battery recycling, ElectraMet has separated itself by removing and recovering high-purity copper from mixed-metal streams while significantly impacting nickel/cobalt stream value by removing trace manganese. The selectivity of ElectraMet cartridges is a result of a decade of research and development. With commercial installations for copper and manganese to below 0.5 ppm without impacting other metals, the selectivity and operational impact cannot be equaled by traditional technologies. The ElectraMet system empowers battery recyclers to maximize metal yields, minimize treatment footprint and complexity, and reduce labor.
Most microelectronics fabs have transitioned from aluminum to copper technology in pursuit of smaller geometries. Due to various process steps in the building and assembly of semiconductors, dissolved metal waste is produced and needs remediation. Per co-founder and CTO James Landon, “Chelators and complexing agents are more prevalent in today’s processes to produce innovative products. Slurries for the polishing steps in semiconductor fabrication use complex chemistries to control the product quality, and the ability to remove the metals from these waste streams continues to be a challenge. ElectraMet systems are purpose built to remove and recover copper and other metals from microelectronics streams.” As semiconductor fabs push towards sustainability, the need to recover metals onsite and eliminate hauling materials to and from fabs is critical.
Redefining Environmental Responsibility
ElectraMet stands at the forefront of environmental stewardship, significantly mitigating the ecological footprint of water treatment processes, particularly through the elimination of sludge production and the associated costs. Remarkably, for every metric ton of copper recovered onsite with ElectraMet technology, the customer prevents the 4.6 metric tons of CO2 emissions that would have otherwise been emitted during mining operations. This reduction in environmental impact is further underscored by the elimination of hauling chemicals or resin into and offsite and the elimination of copper-based sludge disposal.
Intelligent design and material science remove metals to less than one part per million (<1 ppm) while permitting 99.99% water recovery, setting a new standard in the industry.
“Accurate monitoring of metal concentrations aids waste treatment operators in maintaining compliance while data availability alerting production-line operators to potential upsets that may impact product quality and revenue,” emphasizes Dr. Lippert. With a remarkable efficiency rate of 99.99%, ElectraMet removes metal impurities and facilitates their return to end-users for on-site or off-site recycling, further closing the materials loop and promoting sustainability.
Automation plays a pivotal role in streamlining processes, significantly reducing the need for operator intervention, often limited to the harvesting of solid, high-purity metals like copper and silver from the system. Contrastingly, conventional methods relying on chemical additions and precipitation necessitate extensive supervision, including the handling and disposal of sludge waste products.
At the heart of ElectraMet’s success lies its tailored carbon electrode technology, providing a stable interface for metal collection while allowing for customized designs to meet the specific kinetics of various metal separations. Currently, ElectraMet has achieved success in removing a range of metals, including copper, silver, manganese, cadmium, gold, platinum group metals, nickel, cobalt, and lead, with ongoing exploration into new applications.
Flexibility is inherent in ElectraMet’s systems, which can be seamlessly scaled to accommodate the size and requirements of diverse operations. Dr. Landon affirms, “Our modular systems ensure adaptability to many application environments for metals separations. ElectraMet has developed a mobile benchtop unit for deployment to customer sites to demonstrate real-time separations on a small scale, expediting the validation process directly with customers.”
For More Info: https://electramet.com/